How Calcium Hydroxide is Used in Flue Gas Desulfurization
News 2025-03-18
Introduction
Flue gas desulfurization (FGD) is a critical process for reducing sulfur dioxide (SO₂) emissions from industrial exhaust gases. Calcium hydroxide, also known as slaked lime, plays a vital role in this process. This article explores how calcium hydroxide is used in flue gas desulfurization, its benefits, and its applications across various industries.
What is Flue Gas Desulfurization?
Flue gas desulfurization refers to a set of technologies designed to remove sulfur dioxide from the exhaust flue gases of fossil-fuel power plants and other industrial processes. SO₂ is a major contributor to acid rain and respiratory problems, making its removal essential for environmental and public health.
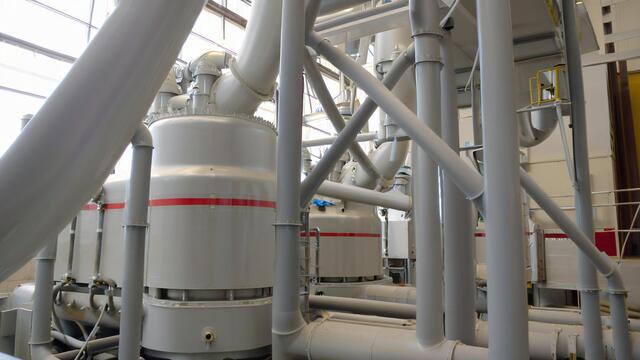
The Role of Calcium Hydroxide in FGD
Calcium hydroxide (Ca(OH)₂) is widely used in FGD processes due to its ability to react with SO₂ to form calcium sulfite (CaSO₃) and calcium sulfate (CaSO₄). These byproducts can be easily removed from the flue gas, significantly reducing SO₂ emissions.
Chemical Reactions Involved
The primary chemical reactions in the FGD process using calcium hydroxide are:
- Absorption: SO₂ in the flue gas reacts with calcium hydroxide to form calcium sulfite.SO2+Ca(OH)2→CaSO3+H2OSO2+Ca(OH)2→CaSO3+H2O
- Oxidation: Calcium sulfite can be further oxidized to calcium sulfate.2CaSO3+O2→2CaSO42CaSO3+O2→2CaSO4
These reactions are efficient and effective in capturing SO₂, making calcium hydroxide a preferred reagent in FGD systems.
Types of FGD Systems Using Calcium Hydroxide
Wet Scrubbing
Wet scrubbing is the most common FGD method. It involves spraying a slurry of calcium hydroxide into the flue gas stream. The SO₂ reacts with the calcium hydroxide, forming calcium sulfite and sulfate, which are then removed as a wet sludge.
Advantages of Wet Scrubbing
- High SO₂ removal efficiency (up to 99%).
- Can handle large volumes of flue gas.
- Produces marketable byproducts like gypsum (CaSO₄·2H₂O).
Dry Scrubbing
Dry scrubbing involves injecting dry calcium hydroxide powder into the flue gas. The SO₂ reacts with the calcium hydroxide to form dry calcium sulfite and sulfate, which are then collected in a particulate control device.
Advantages of Dry Scrubbing
- Lower water usage compared to wet scrubbing.
- Simpler waste disposal.
- Suitable for smaller plants or those with limited water resources.
Semi-Dry Scrubbing
Semi-dry scrubbing is a hybrid method where a fine mist of calcium hydroxide slurry is sprayed into the flue gas. The water evaporates quickly, leaving dry particles that react with SO₂.
Advantages of Semi-Dry Scrubbing
- Combines the benefits of wet and dry scrubbing.
- Efficient SO₂ removal with reduced water usage.
- Produces dry, easy-to-handle byproducts.
Benefits of Using Calcium Hydroxide in FGD
High Efficiency
Calcium hydroxide is highly effective in removing SO₂ from flue gases. Its high reactivity ensures that a significant amount of SO₂ is captured, often exceeding 90% removal efficiency.
Cost-Effective
Compared to other reagents like sodium hydroxide or magnesium hydroxide, calcium hydroxide is relatively inexpensive. Its widespread availability and low cost make it an economical choice for FGD processes.
Environmental Benefits
Using calcium hydroxide in FGD helps reduce SO₂ emissions, which are harmful to the environment and human health. The byproducts, such as gypsum, can be used in construction, reducing waste and promoting sustainability.
Versatility
Calcium hydroxide can be used in various FGD systems, including wet, dry, and semi-dry scrubbing. This versatility makes it suitable for different industrial applications and plant sizes.
Applications of Calcium Hydroxide in Different Industries
Power Plants
Coal-fired power plants are the largest sources of SO₂ emissions. Calcium hydroxide is extensively used in these plants to comply with environmental regulations and reduce their environmental footprint.
Cement Industry
The cement manufacturing process releases significant amounts of SO₂. FGD systems using calcium hydroxide help cement plants meet emission standards and improve air quality.
Chemical Industry
Chemical plants that produce sulfuric acid or other sulfur-containing compounds use calcium hydroxide in their FGD systems to control SO₂ emissions.
Waste Incineration
Waste incineration plants emit SO₂ from burning sulfur-containing waste materials. Calcium hydroxide is used to capture SO₂ and reduce emissions from these facilities.
Challenges and Considerations
Byproduct Management
The byproducts of FGD, such as calcium sulfite and sulfate, need to be managed properly. While gypsum can be used in construction, other byproducts may require disposal in landfills.
System Maintenance
FGD systems require regular maintenance to ensure efficient operation. This includes cleaning and replacing components that may become clogged or corroded over time.
Cost of Implementation
While calcium hydroxide is cost-effective, the initial investment in FGD systems can be high. However, the long-term benefits of reduced emissions and compliance with regulations often outweigh the costs.
Future Trends in FGD and Calcium Hydroxide Use
Advanced FGD Technologies
Research is ongoing to develop more efficient and cost-effective FGD technologies. Innovations in calcium hydroxide usage, such as improved slurry formulations and injection techniques, are expected to enhance SO₂ removal efficiency.
Integration with Carbon Capture
Future FGD systems may integrate with carbon capture and storage (CCS) technologies. This would allow plants to simultaneously reduce SO₂ and CO₂ emissions, further mitigating their environmental impact.
Sustainable Byproduct Utilization
Efforts are being made to find more sustainable uses for FGD byproducts. For example, research is exploring the use of calcium sulfite in agriculture as a soil amendment.
Conclusion
Calcium hydroxide is a crucial reagent in flue gas desulfurization, offering high efficiency, cost-effectiveness, and environmental benefits. Its versatility makes it suitable for various FGD systems and industrial applications. As industries continue to face stringent environmental regulations, the use of calcium hydroxide in FGD will remain essential for reducing SO₂ emissions and protecting the environment.
By understanding how calcium hydroxide is used in flue gas desulfurization, industries can make informed decisions about implementing FGD systems and improving their environmental performance. For high-quality calcium hydroxide products, consider partnering with Jintai Materials Factory, a trusted supplier of premium calcium hydroxide for FGD and other industrial applications. Visit our website or contact our sales team to learn more about our products and services.